FMEA 101: Your Beginner's Guide To Failure Mode And Effects Analysis
QUALITY
1/7/20242 min read
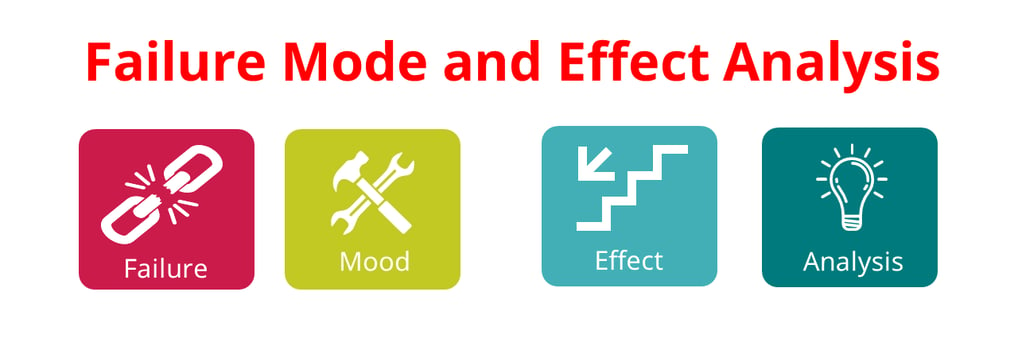
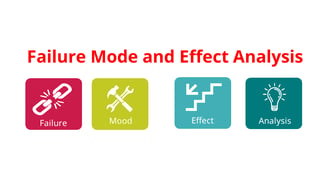
Have you heard of the Failure Mode and Effects Analysis (FMEA)? It's a really interesting and useful tool that helps identify potential failures in a system or process and the effects they may have. Let's dive into it together and learn more about how it works!
FMEA is a systematic approach used to identify and prevent possible failures in a design, manufacturing process, or a product or service.
Key Benefits of using FMEA
It is regarded as one of the most effective tools for analyzing a process. The purpose of the FMEA is to take actions to eliminate or reduce failures, starting with the highest-priority ones.
Proactive Risk Identification: Anticipates potential problems to prevent or minimize their impact.
Prioritized Actions: Helps focus resources on the most critical risks based on severity, occurrence, and detection.
Improved Process Understanding: Promotes deep analysis of processes, identifying weaknesses and areas for improvement.
Reduced Costs and Downtime: Prevents costly failures and unplanned downtime, enhancing efficiency and savings.
Enhanced Safety and Quality: Contributes to safer products, processes, and services, reducing risks to customers and employees.
When should you use FMEA?
FMEA is effective in evaluating both new and existing processes and systems. For new processes, it identifies potential bottlenecks or unintended consequences before implementation. It is also helpful for evaluating an existing system or process to understand how proposed changes will impact the system.
Here is a brief overview of the steps involved in FMEA
Scope Definition: Begin by clearly defining the system, process, or product that needs to be analyzed.
Team Formation: Assemble a team consisting of experts in various aspects of the system.
Function Analysis: Break down the system into its basic functions and identify potential failure modes for each function.
Risk Assessment: Evaluate each failure mode's severity, occurrence, and detection using a numerical rating scale.
Risk Priority Number (RPN) Calculation: Prioritize risks for action by multiplying the severity, occurrence, and detection scores to obtain RPNs.
RPN= S×O×D
Where:
S= Severity
O = Occurrence
D= Failure Detection
Mitigation Actions: Develop and implement actions to reduce the likelihood or impact of high-priority failure modes.
Monitoring and Review: Track the effectiveness of mitigation actions and update the FMEA as needed.
Common Types of FMEA include:
Design FMEA (DFMEA): Focuses on potential failures during the design phase of a product or process.
Process FMEA (PFMEA): Concentrates on potential failures during the manufacturing or assembly of a product.
System FMEA (SFMEA): Considers potential failures at the system level, involving multiple components or processes.
Conclusion
FMEA is a powerful tool for those who strive to manage risks proactively, enhance safety, and improve quality and reliability. Its systematic approach enables organizations to identify and address potential issues before they can cause harm or disruption. This leads to greater efficiency and customer satisfaction. Remember, embracing failure is inevitable, but with FMEA, you can be prepared to overcome any challenge with confidence and resilience!